En vista de la contracción y deformación del engranaje y la precisión no requerida del orificio del eje del engranaje durante el moldeo por inyección del engranaje de plástico, el diseño optimizado del sistema de compuerta, el mecanismo de desmoldeo y el método de enfriamiento se utilizan para producir el plástico de precisión. equipo que cumpla con los requisitos, mejorando así el rendimiento del equipo. rendimiento.
1. Con el rápido desarrollo de la industria, la gente tiene una gran demanda de cámaras, impresoras y fotocopiadoras en la vida diaria y en la oficina. Los engranajes de plástico han reemplazado gradualmente a los engranajes metálicos. Estos equipos tienen requisitos relativamente altos para la precisión del engrane de engranajes. En el diseño de la superficie de separación de la pieza de plástico del engranaje, los insertos en forma de diente con la misma forma de la cavidad del molde fijo y el diseño del núcleo del molde móvil adoptan un diseño de 1 molde y 1 cavidad. Con el fin de evitar fenómenos indeseables como la insatisfacción y la deformación del moldeo por inyección, el molde adopta un método de inyección equilibrada de tres puntos de puerta de molde de tres placas. Para desmoldar suavemente las piezas de plástico del engranaje sin dejar marcas, se utiliza un pasador de soporte redondo para equilibrar. Al optimizar el diseño de estos tres sistemas, se garantiza la precisión y el rendimiento de los engranajes.
2 Análisis de proceso de piezas de plástico
El engranaje de plástico se muestra en la Figura 1. El material seleccionado es polioximetileno (POM), que tiene buenas propiedades mecánicas, y la tasa de contracción de moldeo es de 2% ~ 3%. Cuando la temperatura del material es alta, cambiará de color. Se debe diseñar el sistema de enfriamiento. La circulación es uniforme y buena, y la temperatura del molde de inyección está garantizada en 80 ℃ ~ 100 ℃.
Como se muestra en la Figura 2, el diámetro exterior máximo del engranaje de plástico es la polea, basado en el orificio del eje medio ϕ 4 mm, el requisito de coaxialidad es ϕ 0,05 mm, y la polea y el orificio central ϕ 4 mm y la tolerancia de forma de desviación total El requisito es de 0,05 mm. La selección de la superficie de partición principal se basa en la superficie superior ϕ contorno máximo de 11 mm, el área de color claro se establece en la parte del molde fijo, y el área oscura y el núcleo de formación del eje intermedio se establecen en la parte del molde móvil, que Puede garantizar la precisión del engranaje de plástico. Las características con tolerancias de forma y posición y tolerancias dimensionales se determinan de acuerdo con el grado MT5, y para tamaños libres, el valor de tolerancia se puede obtener de acuerdo con la tabla de consulta MT7.
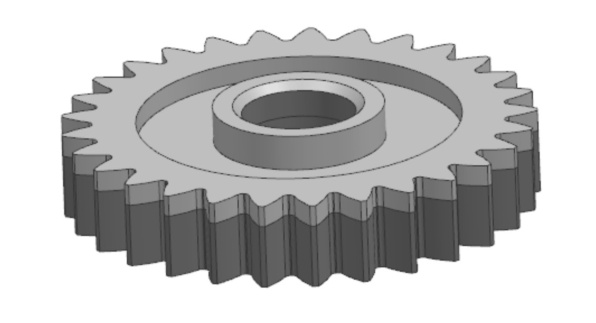
|
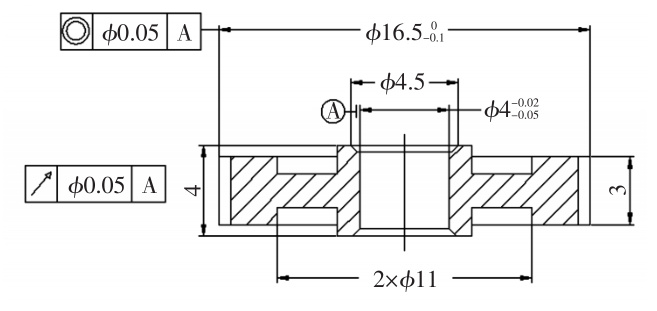
|
3 Diseño de sistema de puerta (1) El diámetro del extremo pequeño del canal principal es ϕ 0,5 ~ ϕ 1 mm según el diámetro de la boquilla de la máquina de moldeo por inyección, el ángulo del cono del canal principal es 2 ° ~ 6 °, la longitud es ≦ 60 mm, y el diámetro del extremo pequeño de la corredera principal del engranaje de plástico es ϕ 2,5 mm, el ángulo del cono es 2 ° y la longitud real es 37 mm. (2) El corredor adopta una sección en forma de U de uso común, H = 1.25R, R = 0.5B, y el corredor de engranajes de plástico H es de 3.0 mm, B es de 3.9 mm y R es de 1.7 mm para hacer el plástico en un estado fundido. Fluye rápidamente hacia los canales y se llena uniformemente, lo que garantiza una buena presión y un llenado uniforme. (3) Los tipos de puertas suelen incluir puertas laterales y puertas de punto. Las puertas laterales solo se pueden diseñar en la superficie de separación principal. El diseño y el procesamiento son convenientes, pero hay marcas de puerta. Para obtener plástico de alta precisión y alto acabado, por lo tanto, se selecciona el método de vertido de tres puertas. La ventaja de la puerta de punto es que no hay necesidad de recortar las rebabas, la puerta se caerá automáticamente y se puede realizar una producción automatizada. El plástico en estado fundido fluye radialmente desde la puerta hacia los alrededores, y se forman 3 líneas de soldadura en la unión de flujo. En la posición de la línea de soldadura, el frente de flujo tiende a ser paralelo y se forma un área de baja contracción a lo largo de la línea de soldadura, que no es fácil de deformar, para obtener engranajes de alta precisión. Para resumir el análisis, combinado con el software de análisis de flujo del molde MoldFlow para determinar el punto de vertido, el diseño del sistema de vertido de engranajes de plástico, como se muestra en la figura. 4 Diseño del sistema de refrigeración Cuando el molde se inyecta en la máquina de moldeo por inyección, el material de la pieza de plástico es POM, que es un material sensible al calor, y es fácil cambiar de color cuando la temperatura del material es alta. Por lo tanto, para controlar la temperatura del material y el tiempo de moldeo durante el moldeo por inyección, debe establecerse razonablemente un sistema de enfriamiento para garantizar que la temperatura del molde se mantenga entre 80 ° C y 100 ° C durante la inyección. La placa decapante está equipada con un circuito de agua circulante, y las plantillas fijas y móviles están provistas cada una de 2 canales de agua simétricos y rectos. El diámetro de la sección transversal del canal de agua es ϕ 8 mm. El diseño del sistema de enfriamiento del molde se muestra en la Figura 4. La plantilla fija y la superficie del diente están provistas de ranuras de escape. Para eliminar el aire atrapado, la profundidad de la ranura es menor que el valor de desbordamiento de plástico y la profundidad de la ranura es de 0,2 mm.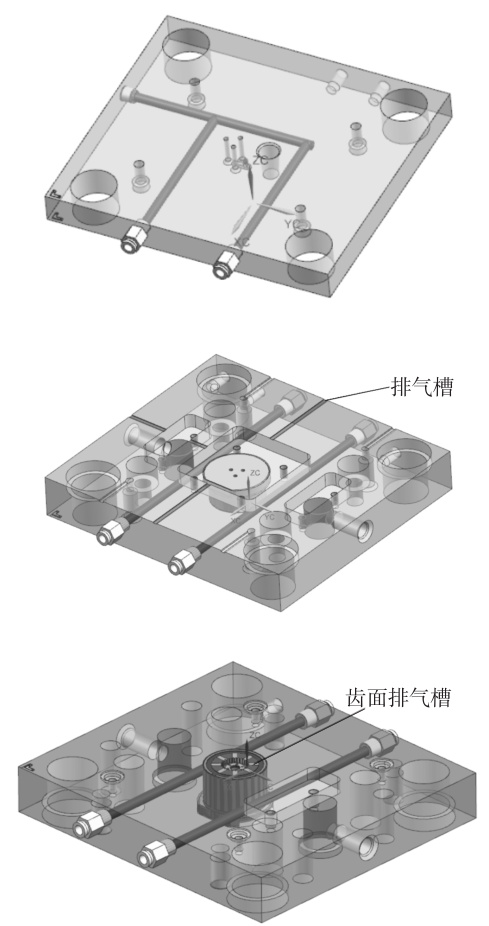
|
6 Lanzó el diseño del mecanismo Los mecanismos de expulsión comúnmente utilizados incluyen varillas de expulsión, cilindros y placas de empuje. La placa de empuje es adecuada para la carcasa y las piezas de plástico que no pueden dejar marcas en la superficie exterior. El cilindro se usa comúnmente para expulsar piezas de plástico cilíndricas, en forma de anillo y perforadas. Este tipo de fuerza de desmoldeo es uniforme y la pieza de plástico tiene una deformación pequeña, pero su precisión es baja. Se puede utilizar para marchas por debajo del nivel 4. Hay un hueco en el medio del cilindro, que aumenta Introduzca el error. La varilla de expulsión puede expulsar las piezas de plástico de manera uniforme. Este tipo de desmoldeo puede garantizar la tolerancia de desviación de las piezas de plástico y la precisión puede alcanzar 3 niveles o más. De acuerdo con las características de la pieza de plástico, se selecciona el pasador de expulsión para empujar hacia afuera, como se muestra en la Figura 6.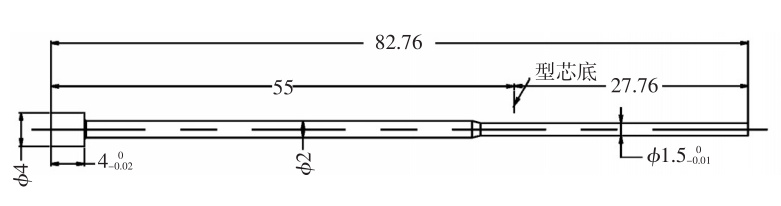
|
7 Estructura de montaje del molde y su proceso de trabajo. La estructura del conjunto del molde se muestra en la figura. Cuando se abre el molde, para evitar que la parte de plástico del engranaje se tense o se quede en el costado del molde fijo, se diseña un resorte 16 en la varilla de tracción pequeña para hacer que la superficie de separación Ⅰ-Ⅰ se separe preferentemente de la Ⅱ -Ⅱ superficie de partición. La puerta se separa de la pieza de plástico del engranaje bajo la fuerza de la varilla 19; el molde móvil se mueve hacia el lado de la varilla superior de la máquina de moldeo por inyección. Cuando el lado izquierdo del escalón del tirante pequeño 11 toca el lado derecho de la plantilla fija 4, la superficie de separación Ⅰ-Ⅰ se mueve Fin; la superficie de partición Ⅱ-Ⅱ se separa como la superficie de partición principal. Debido a la fuerza de embalaje de la pieza de plástico del engranaje, la pieza de plástico permanece en el núcleo del molde móvil. La placa de tracción de posicionamiento en el lado superior del molde limita la distancia de la superficie de separación Ⅱ-Ⅱ (La distancia de separación de Ⅰ-Ⅰ, Ⅱ-Ⅱ puede permitir que la cabeza del material y las piezas de plástico del engranaje se apaguen automáticamente); posteriormente, la superficie de separación Ⅲ-Ⅲ se separa y el material de la puerta se cae; el molde móvil continúa moviéndose hacia la derecha, y el pasador de expulsión de la máquina de moldeo por inyección Empujando la placa inferior de la varilla de expulsión para moverse, la varilla de expulsión expulsa la pieza de plástico del engranaje del núcleo del molde móvil, y la pieza de plástico es automáticamente demolido. Cuando se cierra el molde, el resorte 13 de la varilla de reposición 12 restablece preferentemente el pasador de expulsión y acciona el pasador de expulsión 10 para volver al estado inicial. Se cierra el lado del molde y finalmente se cierra el molde. 8 observaciones finales El molde adopta un método de puerta de punto de molde de tres placas para verter, un molde y una cavidad, y se diseñan tres superficies de separación. El aire es bueno, y se soluciona la contracción y deformación de las piezas plásticas del engranaje. Al diseñar el mecanismo de expulsión, la superficie de separación Ⅰ-Ⅰ tiene prioridad sobre la superficie de separación Ⅱ-Ⅱ. La varilla de tracción y la placa de posicionamiento están diseñadas para limitar la distancia de la abertura del molde. La varilla de expulsión se utiliza para empujar hacia afuera para garantizar la tolerancia de excentricidad de la pieza de plástico. Precisión. Cuando el molde se produce realmente, el mecanismo del molde es estable y confiable, y la calidad y precisión del producto producido cumplen con los requisitos de uso.